Cold / Hot Aisle Containment
Marley Welland-Fulford • October 27, 2022
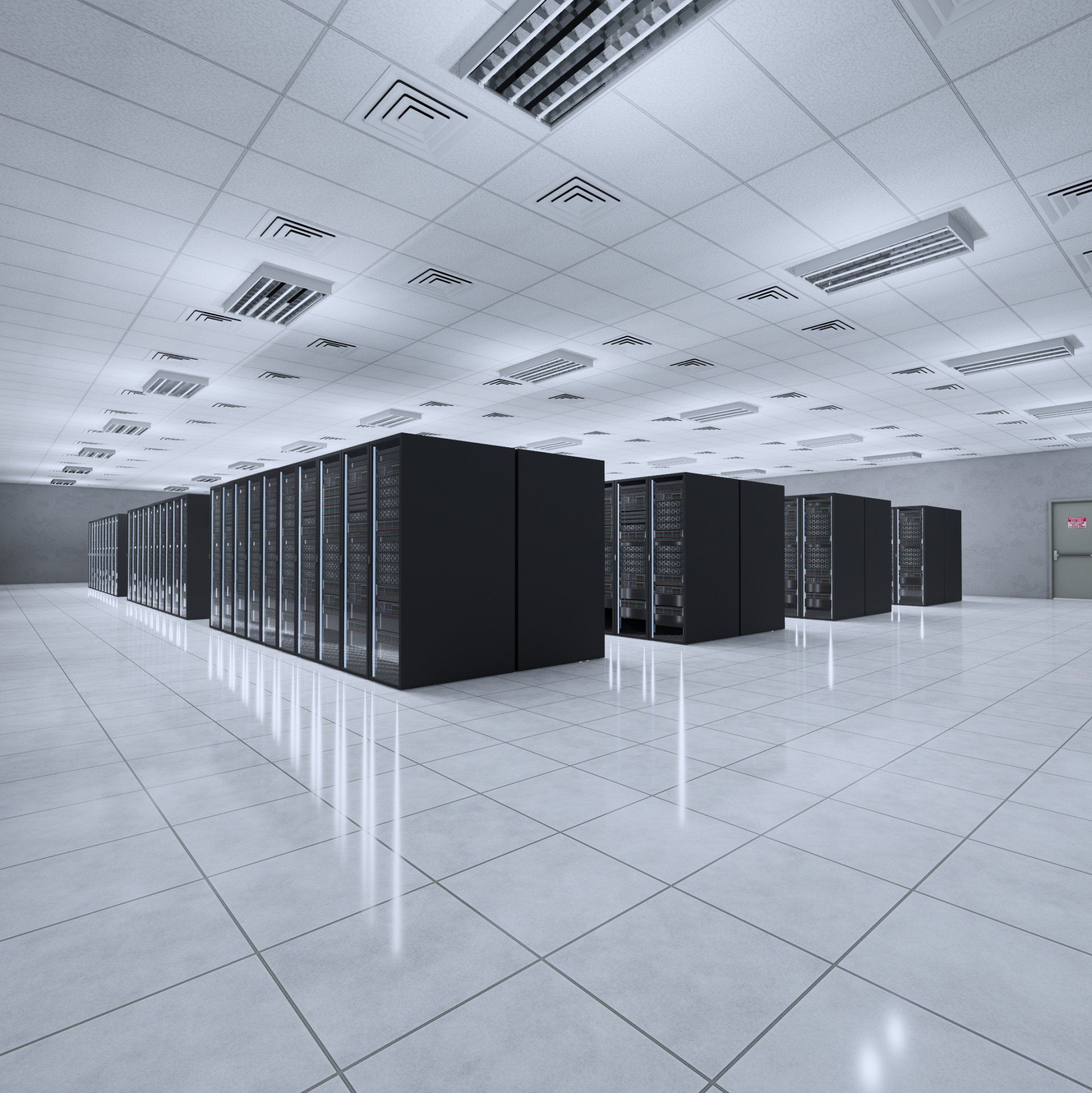
Data Centre Containment and Fire Protection
Due to the ever changing world of Data Centre cooling, there are a variety of approaches and air distribution methods found in today's Data Centre's. It's essential when designing a fire protection system that the key airflow paths and plenums are identified.
The air distribution mechanism will usually present a hurdle for the fire suppression system and the aspirating smoke detection system.
There are 3 common approaches we come across:
The containment dividers in the diagram above are generally vinyl transparent plastic sheets. While these plastic sheets serve to control and contain airflow, they can cause complications with fire protection systems in terms of partitioning and disrupting discharge patterns.
Gas Suppression
Where Cold Aisles are part of the room being protected, we try to include nozzles in the aisles wherever possible. This is because of a requirement in BS EN 15004 that “the type, number and placement of nozzles shall be such that the design concentration is achieved in all parts of the enclosure”.
The cold aisle would be shielded from the direct discharge pattern of the room nozzles. We have, therefore, adopted a holistic approach to protecting the entire risk whereby the designer will treat cold or hot aisles as similar to enclosures such as floor voids or ceiling voids, areas where nozzles are considered necessary to achieve a homogenous mixture of agent throughout all enclosures.
One further consideration is that halocarbon agent nozzles need a certain level of clearance in the horizontal plane of the nozzle orifices in all directions in which the nozzle directly discharges (to both sides and in front of the nozzle for the 180° variant).The optimal location for the nozzle is therefore in the centre of the longest wall of the cold aisle, with at least 1.2m clearance to either side and in front of the nozzle. If a wall or other significant obstruction is within 1.2m of the nozzle’s direct discharge pattern, additional agent will be needed to compensate for expected loses.
Aspirating Detection
Contained aisles use a supply and return air distribution system, where the IT equipment supply or return airflow is completely or partially enclosed to minimise air mixing. This contained approach is recognised as hot aisle/cold aisle configurations. For reasons of energy efficiency and cooling effectiveness the contained approaches using hot and cold aisle designs are now common approaches found in data centres.
Ceiling sampling points are recommended for fire sources outside of IT cabinets. Direct sampling of the hot air return ducts or the interior of the equipment cabinets are areas for placement of sampling.
Although spot detectors are considered for these containment applications, their performance can actually be degraded by high airflow and the limitation of being able to detect smoke at a spot location rather then passing matter, aspirating detection can overcome these limitations. Outputs from the aspirating detection systems can be useful for the automatic release of vinyl curtains, allowing them to open prior to operation of the fire suppression system.
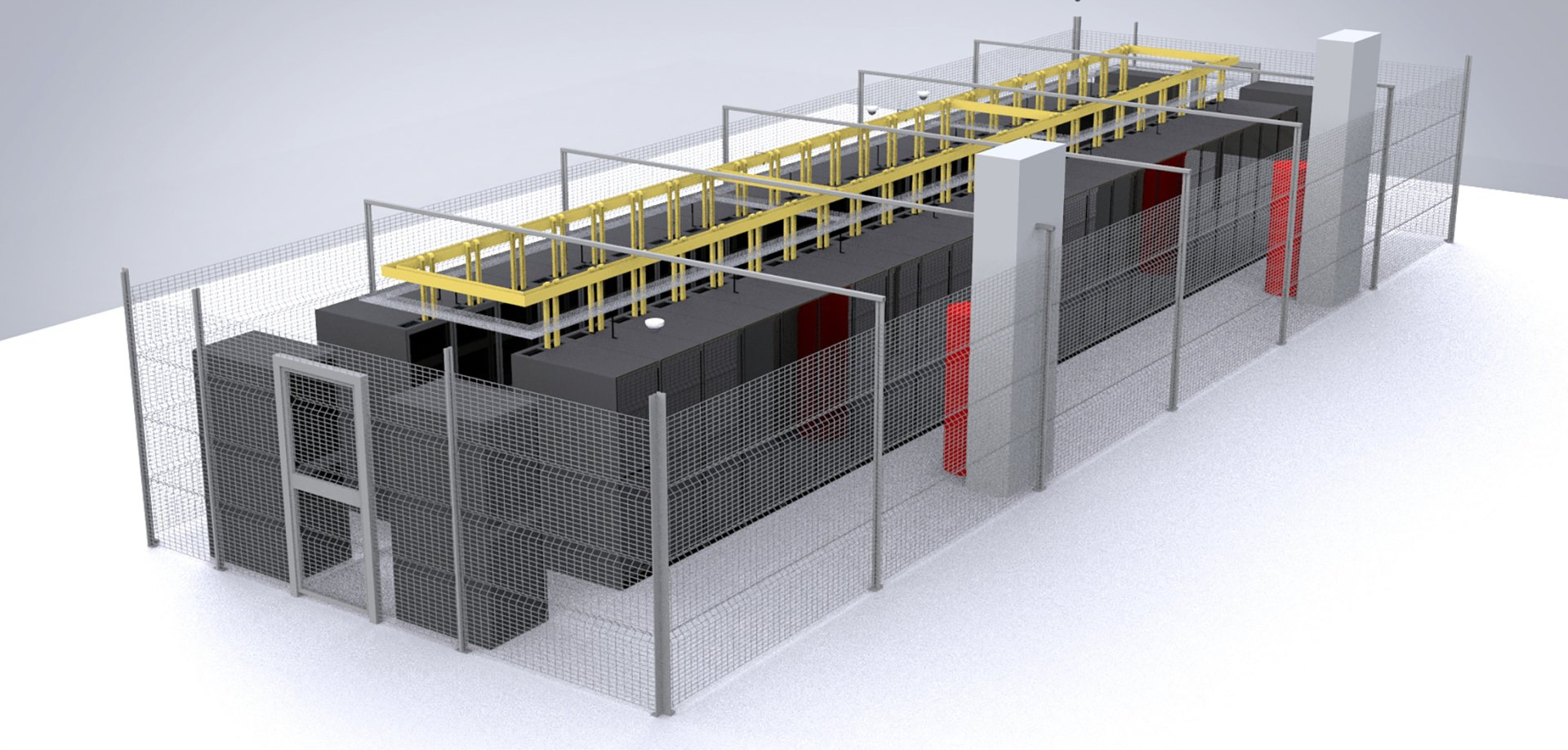